电池、电机、电控技术是电动汽车的三大件,这三块决定了一款电动汽车的性能与质量。而电控技术的核心,便是 BMS 系统,BMS 系统是影响电动汽车续航里程与充电时长的最重要的因素之一。它负责对电动汽车的动力电池进行安全监控和有效管理,让动力电池在最佳的状态下工作,提高动力电池的效率和可靠性并延长它的使用寿命。
在以动力电池为能量源的电动汽车中,BMS 作为连接电池组、整车系统和电机的“纽带”,其重要性不言而喻。随着电动汽车销量不断增加,BMS 的市场规模也在不断扩大,2018 年全球 BMS 产值规模 53.1 亿美元,2019 年全球 BMS 产值规模超过 60 亿美元;预计 2025 年全球 BMS 产值规模将达到 111.7 亿美元。
那么,未来几年,BMS 技术将会呈现怎样的发展趋势?与非网策划的《BMS 的新使命》专题中,我们邀请了瑞萨电子中国汽车解决方案事业部技术市场经理张玮先生,他负责瑞萨电子中国区 BMS 市场推广和应用。
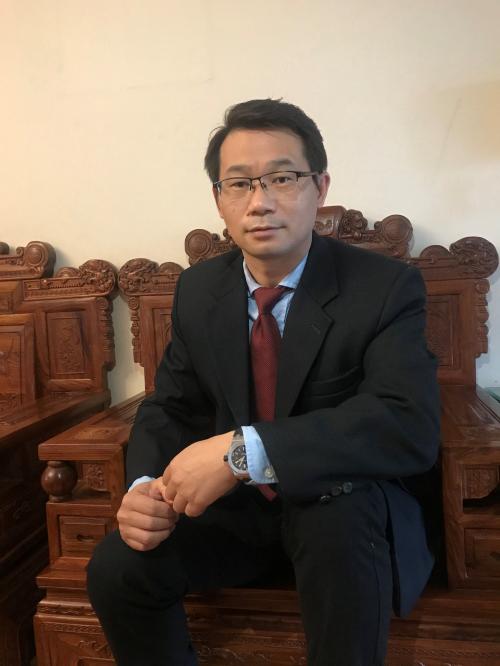
瑞萨电子中国汽车解决方案事业部技术市场经理 张玮先生
BMS的四项核心技术优化电池续航和充电问题
相对燃油汽车,续航里程短、充电时间长一直是电动汽车的痛点,BMS 作为电池管理系统在续航里程和充电长时间改善上起着重要作用。BMS 首先要对动力电池的状态进行实时、精准地监测,接下来要在监测数据的基础上对电池状态(如 SOC 剩余电量和 SOH 电池健康程度)进行评估,以确定合适的控制策略,确保电池组在安全的工作状态下,完成充电、放电和配电的过程,最大限度地优化电能的使用、延长电池的寿命。
关于电动汽车的续航里程和充电时间优化,张玮从技术角度分析了 BMS 系统的几项核心技术:
第一项便是电池状态估算技术,这项技术可以基于电池的精确建模和参数监测。通过大数据分析和先进的算法,对 SOC、SOH、SOP 等电池状态进行准确的估算,为电池管理提供可靠的基础。
第二项便是均衡管理技术,电动汽车的锂电池组中单体电池的不一致性会极大影响电池组的可用容量,这就需要通过均衡管理技术(通常包括被动均衡和主动均衡两种技术)提到单体电池的一致性,提升电池组的使用寿命。
第三项是 BMS 系统的分布式架构,分布式的 BMS 系统将电池模组和电池采集单元集成在一起,让电池组更加模块化、标准化和智能化,扩展性更强,还可简化装配过程、便于实现电池的梯次利用。
最后一项便是将 BMS 技术与整车控制器(VCU)功能的集成,这项技术可以由 VCU 根据整车信息和电池信息采取更合理和高效的控制策略,对于可提升实时性、安全性和可靠性也很有帮助。
延长电池寿命的有效方式
电池寿命一直是电动汽车面临的重要课题,业界一直在针对提高电池使用寿命进行技术研发。到目前为止,最行之有效的就是 BMS 技术,这项技术能够在电池充放电过程中,实时采集动力电池组中的每块电池的端电压和温度、充放电电流及电池包总电压,防止电池发生过充电或过放电现象。同时能够及时给出电池状况,挑选出有问题的电池,保持整组电池运行的可靠性和高效性,使剩余电量估计模型的实现成为可能。除此以外,BMS 还将建立每块电池的使用历史档案,为进一步优化和开发新型电池、充电器、电动机等提供资料,为离线分析系统故障提供依据。
针对瑞萨的 BMS 技术,张玮介绍,“瑞萨电子也推出了令人印象深刻的 BMS ISL78714 电池管理 IC,此款方案可以提供精准的电池电压与温度测量、电池均衡及广泛的系统诊断,目的是更好的保护 14 节锂电池组,最大限度的提升电动汽车的电池寿命和续航里程。”
他强调,“与传统 BMS 相比,瑞萨电子赋予了 ISL78714 更多技术优势,其可监测并均衡多达 14 个串联电池,在汽车工作温度范围内测量精度可达±2 mV,能够更加完善的帮助系统设计人员根据绝对电压水平进行判断。在做到高性能的同时,ISL78714 保证了电动汽车电池组系统的安全性与可靠性,使汽车制造商能够达到 ISO 26262 汽车安全完整性等级(ASIL D)评估。”
BMS的整合和优化
随着电动汽车的不断发展,BMS 技术也不断成熟,未来的 BMS 技术也将更加智能化和数据化,而那些进行更多的 BMS 试验开发、制造以及梯次利用等环节实验,并且有详细的电池数据的 BMS 企业将更具竞争力。
功能安全领域未来也将是 BMS 发展的重点,一款新的 BMS 在投放市场前需要经过严格的环境可靠性测试,其周期可能长达数年,在一些简单的实时监测功能上需要添加产品功能的可靠性、稳定性、精准度、使用寿命等更加严格的测试标准。
瑞萨电子认为,安装优秀的电池管理学 BMS 能够有效提高电池的利用率,防止电池出现过充电和过放电,并且延长电池的使用寿命,监控电池组及各电池单芯的运行状态,有效预防电池组自燃,如遇紧急情况提前对司机做出突发事件预警,为保障安全赢得时间。
芯片厂商如何应对BMS技术带来的挑战?
众所周知,电动汽车的核心是电池,而电池的核心在电池管理系统。电池管理系统作为实时监控、自动均衡、智能充放电的电子部件,起到保障安全、延长寿命、估算剩余电量等重要功能,是动力和储能电池组中不可或缺的重要部件。随着电动汽车的不断发展,BMS 技术也将迎来新的技术挑战。
作为近年来兴起的技术,BMS 的技术门槛是相当高的。没有长期研发的积累和大量数据的沉淀,难以开发出优质的产品,因此,BMS 研发需要大量的时间与资金支持,导致了目前 BMS 研发技术参差不齐。
张玮强调,“对于大多数芯片厂商来说,BMS 的发展都需要经过大量实践,比较容易受到资金限制,所以,BMS 行业需要规范自身研发标准,提升研发效益。芯片厂商们也要增强核心零件自我生产能力,与其他企业合作研发,争取能够实现全新的 BMS 行业联盟。”
保持电池系统创新应对安全问题
自新能源汽车走入大众生活以来,发生起火和自燃事件是屡见不鲜,每次事故都备受市场关注,这也引发了大众对于新能源汽车安全方面的众多思考。电动汽车的动力来源正是来自于一个个小的电池个体,举例来说,一辆电动汽车的电池组里面有着几千节锂电池单体。那么可以想象如此多的电池单体,每一个都是单独制造,即便是生产线产物,也难免在一致性上出现问题。而且在后期的复杂环境中使用,难保会有某一节电池单体出现问题,从而导致整个电池组乃至整个动力电池单元的损坏。
BMS 系统是电动汽车不可或缺的重要部件,是管理和监控动力电池的中枢,管理、维护、监控电池各个模块,肩负着防止电池过充过放电、延长电池使用寿命、帮助电池正常运行的重任。
张玮介绍,“目前瑞萨电子拥有为满足汽车级 (AEC-Q100)打造的锂离子电池管理解决方案 (BMS),该解决方案是专为满足新一代电动汽车应用的严格安全性、可靠性和性能要求而设计。我们的电池平衡和安全产品组合采用高度集成的 ISL78714、ISL78600 和 ISL78610 锂电池管理系统和安全监控 IC,具有众多优势,并显著减少混合动力、插电式混合动力及电动车 (HEV/PHEV/EV) 电池组及其相关系统的总体电池管理成本。”
除此之外,瑞萨电子还提供 ISL78692和ISL78693汽车级单芯电池充电器,可延长车载紧急呼叫(eCall)系统中使用的锂离子 (Li-ion)、锂聚合物 (Li-polymer) 和磷酸铁锂(LiFePO4)电池续航时间。此外,在 Formula E 赛事上,瑞萨电子还为马恒达车队设计并开发了 BMS 模块包括汽车级 BMS 组件,外壳和锂离子电池。此外,创新的低压 BMS 模块还为其高功率处理器 RH850/E2x 微控制器(MCU)提供了足够的额外处理带宽,以支持未来的低压电池系统创新。
“与非管理型低压锂离子电池系统相比,瑞萨 Formula E BMS 模块提供了显著的安全性改进,同时提高了低压系统的整体效率和可靠性。我们在开发 MS 时采用的模块级方法,需要定制设计电路原理图、PCB、硬件组件、软件以及对每个组件和整个模块进行严格测试。我们的低压 BMS 技术的增强性能和功能最终可以为电动汽车带来一系列的设计、开发甚至是商业改进。” 张玮最后表示。
|